Proviamo a realizzare un serbatoio in kevlar
- sandrocacciola
- 2 feb 2023
- Tempo di lettura: 6 min
Salve amici, apro questo mio nuovo thread per condividere con tutti gli appassionati di questo hobby le mie esperienze, tecniche, sbagli e suggerimenti. Quello di cui voglio parlarvi oggi è la realizzazione di un serbatoio in kevlar per una jet a turbina che allestirò a breve: un “Predator” 2,2mt di PilotRc. Anche se ci sono in rete diversi video su questo argomento, il mio thread vuol essere “terra terra”, semplice semplice, realizzato non da n professionista ma da un modellista che continua ad avere la passione nel “provare” e mettersi alla prova.
Partiamo dal modello: per questo serbatoio mi sono ispirato a quello che PilotRc commercializza separatamente per il suo “Predator 2,2”, un serbatoio con Uat (sempre pieno) integrato da 4,6 Lt. L’idea mi è venuta in quanto da pochi mesi ho acquistato una stampante 3D ed è proprio con questa stampante che ho realizzato gli stampi del serbatoio. Il problema è stato trovare i disegni di questo serbatoio e poi convertirli in 3D ma fortunatamente mi sono vebuti in aiuto alcuni utenti di un forum specializzato in stampa e disegno 3D (https://www.stampa3d-forum.it/). Una fucina di idee e di persone non solo capaci ma soprattutto disponibili. Ho postato le foto formato Cad 2D di questo serbatoio e in qualche giorno e svariati ritocchi e modifiche ecco pronto il formato “Stl” del mio serbatoio e dello Uat. Ridotto leggermente perché avesse una capacità di circa 3,5Lt (più che sufficienti per la mia turbina 120N) il serbatoio è stato disegnato la parte principale in 4 gusci (due metà per la parte inferiore (che ha anche una svasatura dove si infilerà la parte superiore per chiudere i due gusci con una giunzione perfetta) e due metà per quella superiore per consentire alla stampata di poter essere estratta facilmente dal master.
Ottenuti i file ho iniziato a fare qualche prova di stampa sulla mia Artillery Sidewinder X2 per trovare (io utilizzo come slicer “Cura”) i parametri giusti che consentissero di avere una superficie dello stampo interna più levigata possibile. Una volta trovata la configurazione ottimale ho iniziato a stampare gli stampi. Sono state necessarie circa 55 ore di stampa per ottenere tutti i pezzi ed a questo punto mi sono dedicato al lavoro di finitura.
I pezzi stampati con la stampante 3D per quanto siano precisi e di qualità hanno piccole scalettature che se non corrette lascerebbero le impronte sul pezzo stampato. Dunque ho carteggiato gli interni prima con carta vetrata da 120, poi 200 e infine 360. Ho dato poi una bella mano di stucco a spruzzo catalizzato e poi una verniciata con vernice acrilica 2K. Il risultato sono state superfici a specchio!
Chi ha un po’ di dimestichezza cvon gli stampi in compositi sa che ogni stampo nuovo deve essere trattato con distaccante prima della stampata. Dunque vi dovete procurare una cera distaccante per stampi (la trovate in tutti i negozi online di articoli modellistici o di lavorazione di compositi (io mi servo da Sorvolando Compositi “sorvolandocompositi.it” costo circa 25 euro per un barattolo da 400/500grammi che vi dura una vita e, cosa che crea valore aggiunto, una persona che sa darvi tanti utili consigli). Questa cera deve essere applicata all’interno dello stampo con un panno di cotone morbido con movimenti circolari stando attenti a trattare tutti i punti dello stampo e la parte superiore dove il tessuto e la resina strasborderanno). 7/8 mani di cera (ogni mano intervallata da una asciugatura all’aria di una ventina di minuti e leggera lucidata) per uno stampo nuovo sono sufficienti. Nelle stampate successive potte dare un paio di mani sole di cera. Io dfopo la cera utilizzo anche l’alcool polivinilico dato con pistola /aerografo a spruzzo: è un ulteriore agente distaccante che forma una pellicola solubile in acqua e che aiuta l’estrazione del pezzo stampato (qualcuno non lo utilizza).
A questo punto sarete pronti per iniziare a preparare la resina ed il tessuto per la laminazione del serbatoio. Per il tessuto ho deciso di utilizzare un primo strato di Kevlar da 170gmq e due strati di tessuto di vetro da 160gmq. La scelta si è rivelata giusta in quanto ho ottenuto un serbatoio leggero e resistente. E qui però è sorto il primo problema che non avevo considerato: quanto sono andato a tagliare il Kevlar mi sono ritrovato con forbici e cutter elettrico che uso normalmente inutilizzabili. Ho provato con diversi tipi di forbici ma senza riuscire a tagliare il kevlar. Mi sono messo in cerca di un sistema efficacie ed ho scoperto che per questo tipo di tessuti aramidici (come anche in parte il carbonio) occorrono forbici speciali. Ho trovato per puro caso sul web un’azienda con prodotti 100% certificati italiani che produce solo forbici (si chiama “Millemetri” - https://millemetri.it). Propone una vasta gamma di forbici ma quello che interessava a me era la linea “Technik” specifica per utilizzo industriale nel taglio di fibre composite come kevlar, fibra di vetro e fibra di carbonio. Li ho contattati e mi hanno consigliato la forbice “Art. 329 - Sarto 9,5 Aramid” da 24cm (9,5 pollici) di lunghezza. Forbice sarto, misura 9,5” (24,5 cm) con lame e viti in acciaio speciale 62 HRC con microdentatura (su una o entrambe le lame a scelta) ideale appunto per il taglio fibre aramidiche - Kevlar, fibra di vetro, fibra di carbonio. Le ho ordinate e… spettacolo! Taglio perfetto, preciso, senza sfilettature del tessuto, una goduria… Attenzione però perché l’azienda si è raccomandata (come ho scoperto poi essere riportato anche sul sito) che di fondamentale importanza per queste forbici (e in generale su tutte) è la manutenzione: semplici accorgimenti che possono evitare fastidiosi problemi a lungo termine. Viene consigliato dopo l’utilizzo evitare di lasciare sulla lama residui di qualsiasi tipo, compresa acqua o sporcizia in genere; pulire periodicamente le lame aprendo le forbici e oliandole nei punti di scorrimento tra le lame con olio lubrificante (ottimo l’olio di vaselina di grado farmaceutico).
Risolto il problema del taglio dei tessuti vi dovrete preparare dei pezzi di kevlar e di tessuto di vetro che si adattino allo stampo e che lo ricoprano tutto strasbordando un po’ (l’eccesso lo rifilerete una volta posato tutto il tessuto sullo stampo). Lascio a voi la scelta della resina epossidica (mai usare il poliestere perché ritira e puzza da morire) ma consiglio i negozi specializzati (costo di 1kg di resina + catalizzatore dai 20 ai 30 euro a seconda dei marchi). Io per questo serbatoio ne ho utilizzata circa 160 grammi di cui un 10/15% va persa con tessuto in eccesso.
Il lavoro di laminazione inizia adesso (cercate di lavorare in un ambiente con temperatura non inferiore ai 18 gradi altrimenti la catalizzazione sarà rallentata): miscelate resina e catalizzatore con una bilancina di precisione e con un pennello morbido iniziate a spargere la resina all’interno dello stampo; prendete la prima pezza di Kevlar che avete tagliato e disponetela con le mani dentro lo stampo facendola aderire bene con le dita alle pareti (usate i guanti in lattice!!), quindi con il pennello imbevuto leggermente di resina picchiettate sul tessuto impregnandolo bene (vi accorgerete dove è impregnato e dove no dal cambiamento di colore che diventerà scuro dove ha assorbito la resina. Fatto questo passate a stendere il secondo strato con la pezza di tessuto di vetro e con lo stesso procedimento fatelo aderire allo stampo e impregnatelo bene. Fatto questo anche per il terzo strato il lavoro è quasi ultimato. Per rendere l’interno del serbatoio il più liscio ed uniforme possibile dovrete utilizzare un pezzo di tessuto Peelply che ha la particolarità di non attaccarsi permanentemente alla resina ma di poter essere rimosso una volta essiccato portando via la resina in eccesso e rendendo uniformi le superfici (costo pochi euro per 1mq). Lo stendete come gli strati precedenti nello stampo senza però cospargerlo di resina: lo adagiate con le mani e con un pennello senza resina lo fate aderire bene.
Ora avete due possibilità: o lasciare la stampata così come è assicurandovi che tutto il tessuto aderisca bene alle pareti dello stampo per evitare bolle, oppure procurarvi un dispositivo per il vuoto e mettere tutti i pezzi dentro un sacco di nylon apposito e lasciare che il vuoto comprima tutto il tessuto contro lo stampo riproducendo esattamente la sua superficie. Ma qui si apre un capitolo a parte…
Una volta laminato il tutto lasciate catalizzare a temperatura ambiente per 24 ore e poi aprite gli stampi. Il pezzo uscirà con il minimo sforzo (un po' più duro sarà il pezzo nello stampo più piccolo, ma ce la farete. Una volta estratti i pezzi dovrete rifilarli e infine accoppiarli. Avrete così il vostro serbatoio finito. Vi resterà da scegliere che attacchi desiderate utilizzare per le linee carburante, ma questa è una scelta soggettiva.
Buon divertimento!!!











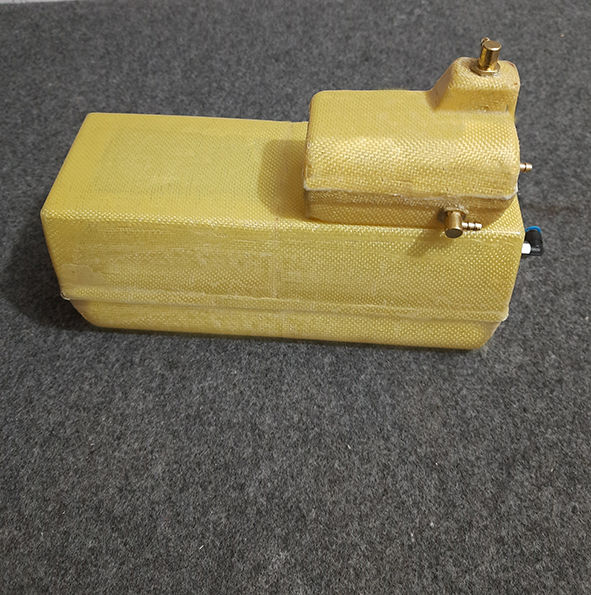
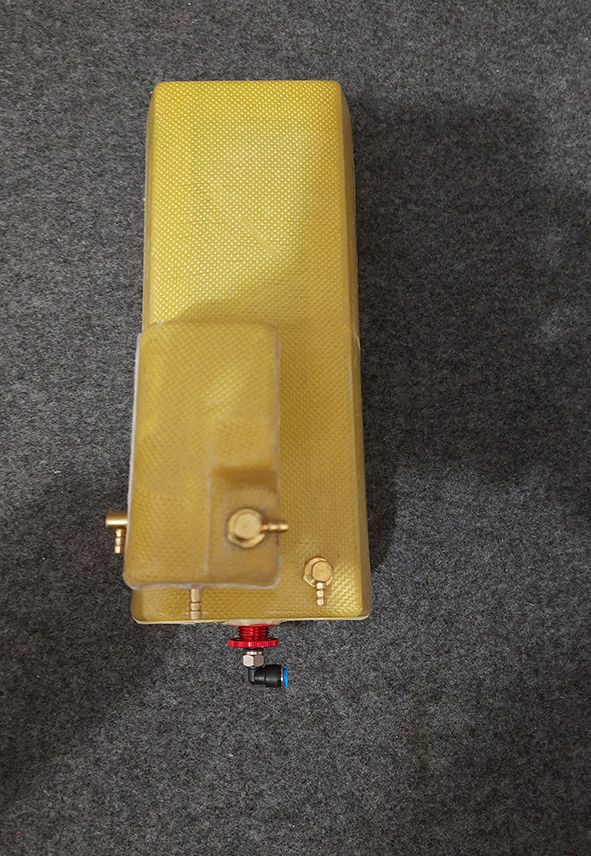
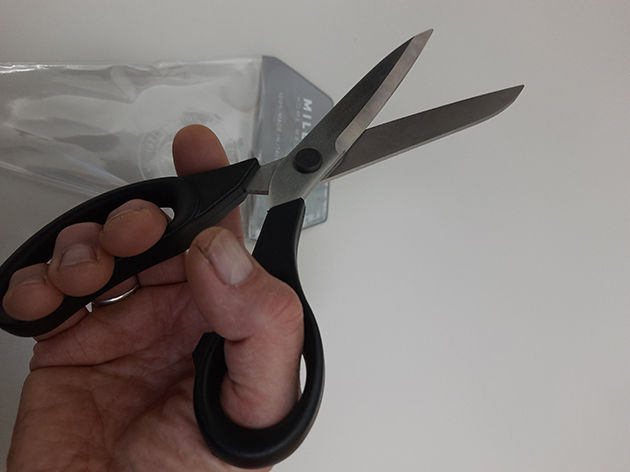

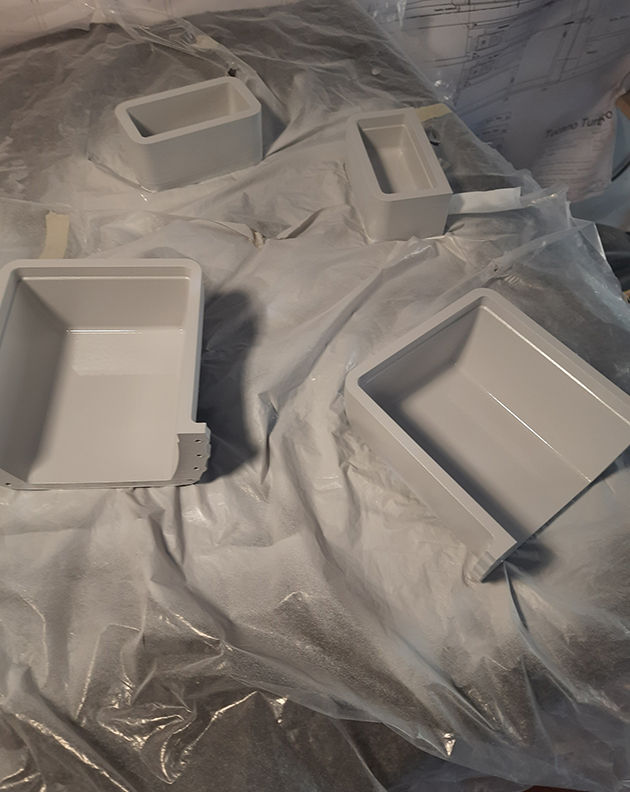
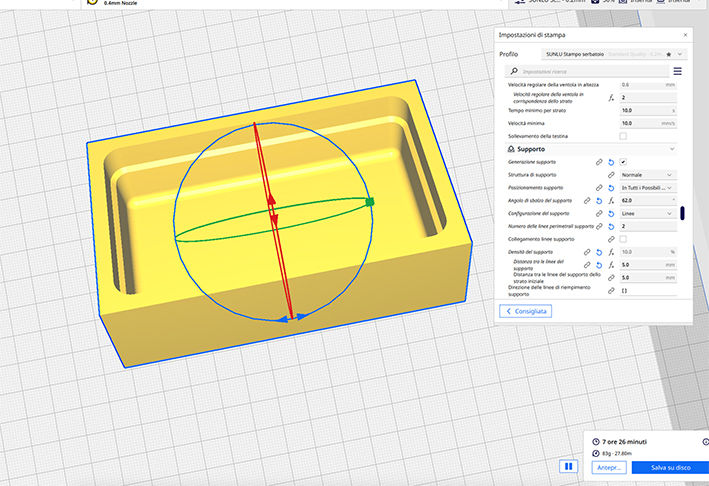
Comments